Marina-C

Desalt C is available for both indoor and outdoor use. All the desalination components are pre-assembled in 1 to 2 containers, including the piping and control systems, which considerably reduces the on-site installation workload and time required for effective fresh water production. The design and manufacturing of the system comply with ASME, ASTM, IEC, and other internationally recognized industry standards. The fresh water capacity of fastROC is 50 to 2,000 m3/day (2,040-83,270 liters/hour).
1 Description
iDesalt C series watermaker is designed to produce high quality portable water from sea water or high salinity brackish water.
Together with our 2 pass RO or even EDI system, we could provide highly pure water for industrial or commercial usage.
C series watermaker produce pure potable water from 60 to 1000 ton (15 -260 thousand gallons) per day.
iDesalt C series watermaker is a containerized desalination system based on reverse osmosis principle which is the most popular water treatment technology in the world.

Note: The image shown here is indicative only. The actual product may differ.
C series watermaker is designed to install the pretreatment system, RO system, chemical cleaning system and chemical dosing system all into the container. Containerized design minimize the site installation and erecting time of the desalination system. No need extra roof for the system.
Containerized system also make the transportation much easier.
To ensure the reliability of the watermaker, the core parts are from the well-known manufacturers in water treatment area, such as Danfoss, LG Nano, ROPV, Siemens, Schneider, ABB, etc.
iDesalt watermaker are designed and manufactured on the basis of the industrial standard: ASME, ASTM, IEC, etc.
2 Process
The seawater is taken by an intake pump and sent to a feed tank (if seawater is taken from a very close place and the water turbidity is quite low, seawater could be sent directly to the Watermaker).
Seawater from feed tank is boosted by feed pump and is sent to media filter to remove particles. After too pass cartridge filter, seawater is pressurized by high pressure pump and sent to membrane. Thus we got fresh water, while the same time the concentrated water is discharged directly. Please refer the following process flow diagram for more details.

Note: the diagram is for system with energy recovery device.
3 Features
Containerized design minimize the site installation and shorten the erecting time. Containerized system save cost from transportation and site civil works.
Simple process, feed pump is used as backwash pump for media filter.
Automatically backwash system for media filter.
3 step filtering ensure the safe operation of high pressure pump, energy recovery device and RO membrane.
Super duplex high pressure pump using axial piston principle from Danfoss, higher efficient, lighter, more compact than common plunger pump, and only one service is needed for up to 3 year.
Super duplex energy recovery device using isobaric pressure exchanger principle from Danfoss, much higher efficient than energy recovery turbine, and only one service is needed for up to 3 year.
High pressure hose lower the vibration and noise level, simplify the pipe connection.
Sch40 duplex high pressure pipe (EN1.4462/UNS S32205) and fittings, long life and highly corrosion resistant.
Low fouling, high salt rejection, low pressure RO membrane from LG Nano.
5 layers of corrosion resistant paint protect carbon steel frame and container salt fog leaking water. A hardwearing plastic floor cover avoid the damage of the paint.
Siemens, ABB or Schneider parts ensure the reliability of the control system.
For C-E series watermaker, 10 inch touchscreen is integrated, ease the operation.
Optional intake pump and feed pump.
Optional insulation decoration kit for container
4 Application
Island residential
Hotels, resorts
Construction Site
Emergent water supply, mobile water plant High salinity underground water
5 Specification
5.1 Feed Water Requirement
Salinity (TDS) | 20,000-45,000 mg/L |
Temperature | 5-40 °C |
Turbidity | < 5 NTU |
COD | < 10 mg/L |
Ferrous (Fe2+) | < 0.1 mg/L |
Manganese (Mn2+) | < 0.1 mg/L |
Note: if the feed water is not natural seawater or worse than above, please contact us. |
|
5.2 Product Water Quality
Standard 1) | acceptable drinking water quality for WHO (4 edition) |
Conductivity (online monitoring) 2) | < 1000 μS/cm |
Note: 1) If the source water is natural seawater (or salt water) 2) If the water is for clean or irrigating, higher conductivity might be acceptable |
5.3 Technical Data
System without energy recovery device:
Technical Data | Unit | C-60 | C-80 | C-100 | C-150 |
Rated Product Flow 1) | M3/H | 2.8 | 3.5 | 4.5 | 6.5 |
Rated Recovery Rate 1) | % | 35 | 36 | 35 | 35 |
Min Pressure In 2) | barg | 4 | 4 | 4 | 4 |
Max Pressure In | barg | 6 | 6 | 6 | 6 |
Min System Pressure 3) | barg | 20 | 20 | 20 | 20 |
Max System Pressure 3) | barg | 70 | 70 | 70 | 70 |
RO Membrane Spec. |
| 8040 | 8040 | 8040 | 8040 |
RO Membrane Qty. | pcs | 5 | 6 | 8 | 12 |
Membrane housing Qty. | pcs | 2 | 2 | 4 | 4 |
Rated Power 4) | kW | 20 | 25 | 32 | 44 |
Input 5) |
| 3PH 380V AC±10%,50Hz |
Note: 1. The rated product flow and rated recovery rate are based on the design feed (35,000 ppm, 20°C standard seawater), if the feed TDS is lower, higher product and higher recovery rate could be available; If the TDS is higher, the capacity might be cut and the recovery rate might be lower to ensure the safe operation, contact us for details. 2. As the system has no feed pump, an intake pump or feed pump should be added to provide the required pressure. 3. The normal operating system pressure shall be above the minimum pressure. If higher pressure above 70bar is needed, please contact QT for solution. 4. The power consumption at 70 bar, normally lower. The power of intake pump and/or feed pump are not included. 5. Other input voltage and frequency is available on request. |
System with energy recovery device:
Technical Data | Unit | C-100E | C-150E | C-200E | C-250E | C-360E | C-500E | C-600E | C-720E | C-1000E |
Rated Product Flow 1) | M3/H | 4.5 | 6.5 | 9.5 | 12 | 16 | 21.5 | 25.5 | 31.5 | 41.5 |
Rated Recovery Rate 1) | % | 35 | 35 | 36 | 36 | 45 | 45 | 45 | 45 | 45 |
Min Pressure In 2) | barg | 4 | 4 | 4 | 5 | 5 | 5 | 5 | 5 | 5 |
Max Pressure In | barg | 6 | 6 | 6 | 7 | 7 | 7 | 7 | 7 | 7 |
Min System Pressure 3) | barg | 20 | 20 | 20 | 20 | 20 | 20 | 20 | 20 | 20 |
Max System Pressure 3) | barg | 70 | 70 | 70 | 70 | 70 | 70 | 70 | 70 | 70 |
RO Membrane Spec. |
| 8040 | 8040 | 8040 | 8040 | 8040 | 8040 | 8040 | 8040 | 8040 |
RO Membrane Qty. | pcs | 8 | 12 | 18 | 21 | 28 | 42 | 48 | 56 | 70 |
Membrane housing Qty. | pcs | 4 | 4 | 3 | 3 | 4 | 6 | 8 | 8 | 10 |
Rated Power 4) | kW | 17 | 23 | 30 | 36 | 46 | 69 | 75 | 92 | 119 |
Input 5) |
| 3PH 380V AC±10%,50Hz |
1) The rated product flow and rated recovery rate are based on the design feed (35,000 ppm, 20°C standard seawater), if the feed TDS is lower, higher product and higher recovery rate could be available; If the TDS is higher, the capacity might be cut and the recovery rate might be lower to ensure the safe operation, contact us for details. 2) As the system has no feed pump, an intake pump or feed pump should be added to provide the required pressure. 3) The normal operating system pressure shall be above the minimum pressure. If higher pressure above 70bar is needed, please contact QT for solution. 4) The power consumption at 70 bar, normally lower. The power of intake pump and/or feed pump are not included. 5) Other input voltage and frequency is available on request. |
5.4 Dimensions And Weight

Technical Data | Unit | C-60 | C-80 | C-100(E) | C-150(E) | C-200E | C-250E | C-360E | C-500E | C-600E | C-720E | C-1000E |
SF container size 1) |
| In RO | In RO | In RO | In RO | In RO | In RO | In RO | In RO | 40’ | 40’ | 40’ |
SF dry weight (wet) 2) | ton | - | - | - | - | - | - | - | - | 12(+4) | 16(+5) | 18(+6) |
Feed inlet flange 3) |
| - | - | - | - | - | - | - | - | DN125 | DN125 | DN150 |
Filtrate outlet flange |
| - | - | - | - | - | - | - | - | DN125 | DN125 | DN150 |
Waste outlet flange |
| - | - | - | - | - | - | - | - | DN80 | DN80 | DN80 |
RO container size |
| 20’ | 20’ | 20’ | 20’ | 40’ | 40’ | 40’ | 40’ | 40’ | 40’ | 40’ |
RO dry weight (wet) | ton | 6(+2) | 6(+2) | 8(+2) | 8(+2) | 10(+3) | 10(+4) | 13(+5) | 16(+6) | 9(+1) | 10(+1) | 10(+2) |
Feed inlet flange |
| DN50 | DN50 | DN65 | DN65 | DN80 | DN80 | DN100 | DN125 | DN125 | DN125 | DN125 |
Product outlet flange |
| DN32 | DN32 | DN32 | DN32 | DN50 | DN50 | DN65 | DN65 | DN80 | DN80 | DN80 |
Waste outlet flange |
| DN40 | DN40 | DN50 | DN50 | DN50 | DN50 | DN65 | DN65 | DN65 | DN80 | DN80 |
Note: 1) All the containers are standard 20’ and 40’ container. 2) The dry weight includes containers, sands and membrane. Wet weight means the weight when the system is water filled. 3) DIN standard, contact us if you need ANSI standard. |
6 Installation
6.1 Water Intake
iDesalt C series watermaker is designed for taking clean seawater or brackish water.
If possible, beach well intake is preferred to acquire better source water.
clarifier or slow media filter is strongly recommended. Otherwise, the replacement period of filter cartridge and regeneration period of media filter will be shortened.
If the water is from open intake (water taken directly from sea), a feed tank is recommended. Feed tank would help to settle the sands down and provide a buffer of feed water. If there is a feed tank, a low level switch shall be installed to avoid the dry-running of the feed pump.
Inline flocculation by dosing coagulant could be another solution when feed turbidity is high. Submersible pump or self-priming centrifugal pump is recommended as intake pump.
HDPE or FRP pipe is recommended for long distance water supply.
For beach well intake, water could go directly to the containerized system by intake pump. Raw water could go to a feed tank as well, then another feed pump shall be required for the system.
Intake pump and feed pump will be recommended according to site requirement.
For more information regarding water intake, please contact us.
6.2 Watermaker
MEDIA FILTER
3 step filtering is used in iDesalt C series.
The first step is media filter (normally one media: quartz sand). The media filter remove most of particles above 100 micron, but remove much less particles less than 100 micron.
The media filter shall be regenerated periodically to recover its performance. The period is depending on the feed water turbidity. Normally every 3 days we shall regenerate the media filter.
The feed water from feed tank or intake pump is boosted by feed pump and then sent to media filter. The feed pump is also used as the backwash pump of media filter.
Normally the sands are not filled to avoid the possible damage during transportation. Fill the sands after the all the pipes are correctly connected.
CARTRIDGE FILTER
The second step is pre-filter. 3 micron nominal cartridges (effi.: 80-90%) is installed to remove the particles passed media filter.
The third step is main filter. 10 micron absolute (effi.: 99.9%) cartridges (normally pleated cartridges) is installed to ensure the safety operating of high pressure pump and RO membrane.
Using the right filter cartridges is the key to keep the high pressure pump and RO membrane running well.
INSTALLED
Installed the filter cartridges before the system is started.
Note: QT recommends strongly to use the original filter cartridge kit from QT.
RO
The filtered water is pressurized to 50-60 bar and sent to RO membrane by an axial piston pump. The high pressure pump is positive displacement pump, therefore, the feed flow is constant while the
frequency of the various frequency driver (VFD) is constant.
To avoid membrane damage, ΔP between permeate side and feed side shall never exceed 0.5 bar.
The membranes are not installed to avoid drying or bio-fouling due to long time transportation and site construction.
To lower the energy consumption, an isobaric pressure exchanger (energy recovery device) is installed on all types with “E”.
Install the membranes before the system is started.
The product flow and recovery rate of the system without energy recovery device could be adjusted by the pressure adjusting valve on the concentrate pipeline.
For the system with energy recovery device, the product flow could be adjusted by the RPM of high pressure pump. The recovery rate could be adjusted by RPM of the high pressure pump, RPM and low pressure flow of the energy recovery device.
CIP AND DOSING SYSTEM
CIP pump is used as flushing pump and chemical cleaning pump.
All system have 4 sets dosing pump and chemical tank installed for coagulant, biocides, deoxidizer and antiscalant.
When feed turbidity is very low, no need coagulant dosing.
When feed COD is very low, no need biocides (normally NaClO) and deoxidizer dosing. But shock dosing of non-oxidative biocides is recommended.
When system recovery is low (normally less than 35%), no need antiscalent dosing
6.3 Water Tank
If there is a feed tank, at least a low level switch shall be installed to avoid the dry running of the feed pump.
Install a high level switch and low level switch on the product tank and connect them to the control cabinet, then you could run the system automatically according to water level, i.e. auto ON when low level, auto OFF when high level.
hypochlorite or sodium hypochlorite if the water is kept for a time longer than 3 days.
If the product tank is an elevated tank, install a non-return valve on the inlet pipeline to avoid higher back pressure on the membrane.
7 Storage, Service And Warranty
7.1 Storage
iDesalt C series are designed for indoor and outdoor use. The container should be put or stored on a flat, dry and well ventilated place if possible.
Ambient temperature during operating: +2°C to +50°C
If the ambient temperature is lower or higher than above, an insulation kit for container shall be needed.
Storage temperature: -5°C to +60°C – provided that:
She system is drained of water ;
The system is stored “plugged”;
The membranes and filter cartridges are taken out and stored separately.
Do not install membranes and filter cartridges until the system will be started.
Note: The RO membranes should be stored in a dry and well ventilated place without sunshine, and the storage temperature is: 5-35 °C.
7.2 Maintenance
Good maintenance prolong the system life.
FOR SHORT TERM STOP
After the system is stopped, the CIP pump will automatically flush the RO system with product water. Cleaning chemical or biocides could be added in the CIP tank to maintain the RO membrane.
Note: ONLY NON-OXIDATIVE biocides could be added, otherwise the RO membrane will be damaged.
Normally for short term stop like less than 3 days, it will be OK for the system with NO flushing.
FOR LONG TERM STOP
If the system will be standstill for more than 3 days, the system shall be started for short time every 3 days, and flushed with RO product water. The media filter shall be backwashed at the same time.
water thoroughly. Put reserving chemical into CIP tank, recycle the reserving solution in the system. And the system shall be started for short time every 7-10 days, and flushed with RO product water (with reserving chemical inside). The media filter shall be backwashed at the same time to avoid biofouling.
If the system will be standstill for a long time, do a chemical cleaning for membrane, take the membrane out and store the membrane separately in a reserving solution will be another choice.
ROUTINE MAINTENANCE
1. Regenerate the media filter periodically, we recommend backwash and rinse media filter every 3 days or ΔP between inlet and outlet is above 0.8 bar.
2. Change the filter cartridge periodically, we recommend a replacement every 30 days or ΔP between inlet and outlet is above 1 bar (1 bar for pre-filter and 1 bar for main filter).
Note: life of the cartridge in pre-filter may be shorter than the one in main filter.
Note: QT recommends using 5 micron nominal filter cartridge (normally melt-blown cartridge) or better in pre-filter. QT recommends using 10 micron absolute filter cartridge (normally pleated cartridge) or better only in main filter.
3. Maintain the RO membrane with chemicals (like non-oxidative biocides or NaOH) periodically to keep the performance of membrane for C-80, C-100(E) and C-200E.
4. Regular cleaning to remove the dust or salty dirt from the system.
5. Online chemical cleaning,we recommend a chemical cleaning for membrane every 6 months or ΔP between membrane inlet and brine outlet is above 2.5 bar (When the differential pressure switch trigger, the RO membrane should be cleaned to avoid permanent performance loss). Look for the manual for how to clean the membrane.
Warning: Chemical cleaning must be done by authorized service staff or especially qualified and trained personnel.
7.3 Service
In case of irregular function of iDesalt, please contact QT.
7.4 Guarantee
Provided that the equipment has been running according to the QT’s specifications, QT provides 12 months guarantee from date of commissioning, however, max. 18 months from date of production.
8 System Characteristics
Stability and reliability: We have nearly 30 years of experience in the design of desalination systems
Better filtration: 3 steps filtering process including sand filter, pre-filter and main filter to ensure better protection for high pressure pump, energy recovery device and RO membrane
Quick installation and commissioning: Most of the installation is completed before delivery
Long service life: The wet parts are made of duplex, SS904L, UPVC or other plastics and the heavy-duty marine paint is used for frame and container
Easy operation: User friendly control by touch screen with remote control
Fast restoring feature: In case of malfunction, the whole system can be restored quickly by using standard parts
Upgrade on demand: We can add sensors according to customer needs, collect data remotely and provide operational consulting service
9 System Characteristics
Stability and reliability: We have nearly 30 years of experience in the design of desalination systems
Better filtration: 3 steps filtering process including sand filter, pre-filter and main filter to ensure better protection for high pressure pump, energy recovery device and RO membrane
Quick installation and commissioning: Most of the installation is completed before delivery
Long service life: The wet parts are made of duplex, SS904L, UPVC or other plastics and the heavy-duty marine paint is used for frame and container
Easy operation: User friendly control by touch screen with remote control
Fast restoring feature: In case of malfunction, the whole system can be restored quickly by using standard parts
Upgrade on demand: We can add sensors according to customer needs, collect data remotely and provide operational consulting service
10 Process Flow Diagram
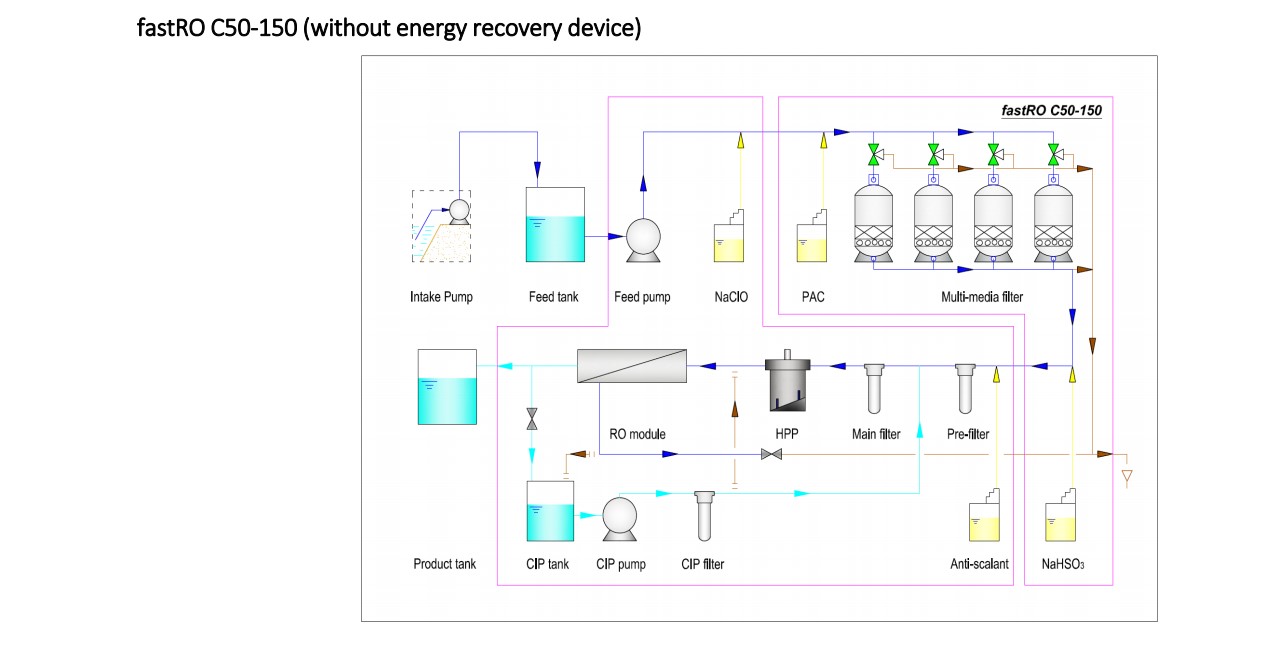
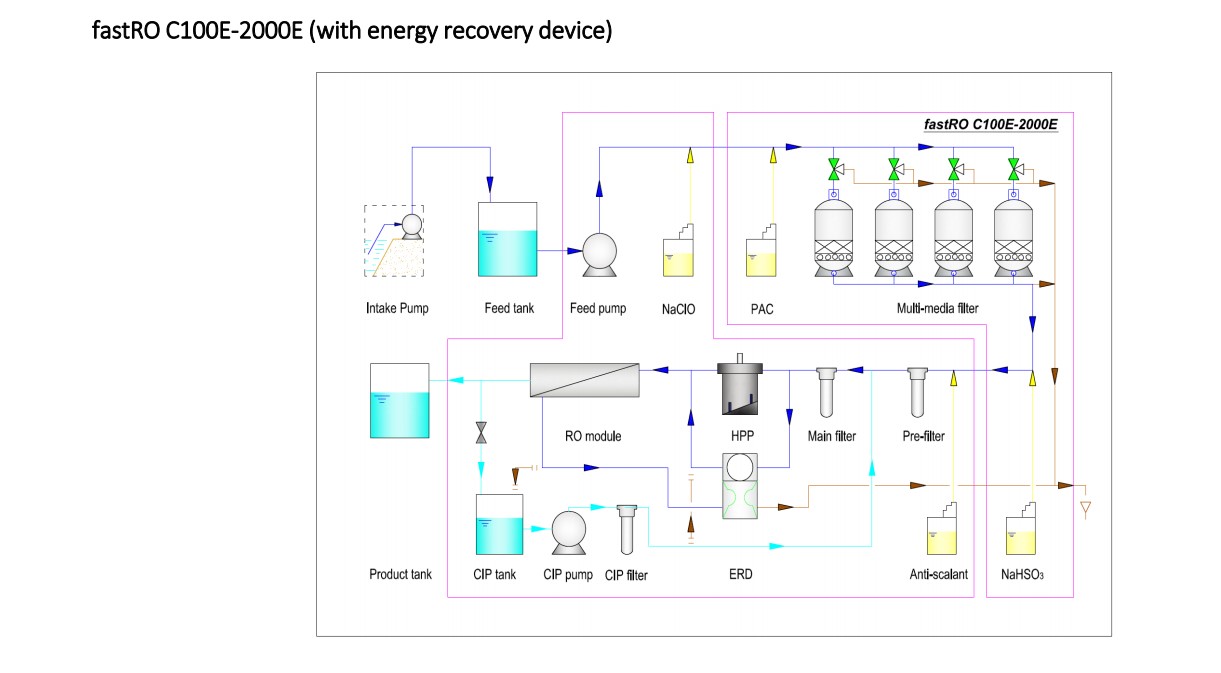
The desalination process is based on Reverse Osmosis (RO) technology. The process starts by filtering particles from feed water through multi-media filter (No need to use multi-media filter if the feed water turbidity is lower than 1 NTU), then entering the high-pressure pump. Fresh water is pressurized out through the membrane, while concentrated water is discharged after pressure relief/energy recovering (by energy recovery device).
11 Product Gallery
